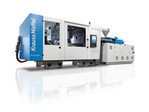
GX with wider platens for packaging applications
During the Open House, KraussMaffei will conduct a live demonstration of a GX 551-4300 ( clamping force 618 US tons) with wider mold fixing platens for packaging and closing applications. In particular, customers from the automotive, packaging and logistics industries are reacting very positively to the new GX series, which is ideally suited to many different injection molding processes thanks to its efficiency and extensive catalog of options as a basis. “Our customers are especially interested in the modular automation cells containing linear and industrial robots in different configurations," said Paul Caprio, President of the US subsidiary KraussMaffei Corporation. “And I would like to emphasize that the GX is the best machine concept on the market!” The GX series currently covers the clamping force range from 450 to 730 US tons in different sizes and equipment variants for the production requirements in a large number of industries. The GX machines are impressive during the production of free falling packaging/logistics parts and premium quality articles for the automotive industry or the consumer goods sector.
High-performance extrusion: Recycling of polyolefins
"In particular, segregated recycling of waste is extremely vital in terms of resource conservation," said Matthias Sieverding, Director of Extrusion Technology, explaining the importance of the exhibited compounding system. The system is specially designed for recycling polyolefins with a residual moisture of up to 10 percent and impurities caused by cellulose residues, adhesive residues, label residues or organic contaminations of up to 8 percent.
Gravimetric metering devices feed the ZE 60 A x 40 UTXi twin-screw extruder with flakes and any additives which are melted in the front section of the processing unit. The extruder features a degassing device to remove the moisture. With a D/d ratio of 1.46, the ZE 60 A x 40 UTXi twin-screw extruder has an optimal balance between free volume and torque. The melt is transferred from the extruder to a Ettlingen melt filter with a constant open filter area and high filter fineness. This melt filter then transfers the cleaned melt to a Gala underwater pelletizer (UWG).
Intelligent co-extrusion solution for efficient and economical production of window profiles
"Our exhibit gives processors a concept with which they can manufacture a premium quality end product using inexpensive raw materials," emphasized Sieverding. The extruder combination comprising the parallel KMD 75-32/P twin-screw extruder and the conical KMD 43 K/P twin-screw extruder produces a double-layered window profile whose core consists of recyclates or highly filled materials. The outer layer is produced using new premium quality material. Output is 120 – 340 kg/h or 30 – 100 kg/h for the coextruder. In cooperation with Greiner Extrusion, KraussMaffei Berstorff supplies the complete line with a corresponding profile mold to the customer Atrium Extrusion Systems, who is totally impressed by the superb quality of the machine and the high system expertise.
Successful integration pays off
By pooling the sales and service activities of the KraussMaffei, KraussMaffei Berstorff and Netstal brands, the KraussMaffei Group combined its strengths and competencies under one organizational umbrella on the American market in October 2012. "Since then, we have been able to offer our customers the right product for them from the right brand and the right services from our extensive service portfolio according to their individual requirements," said Caprio. During the Open House, Netstal will demonstrate the production of a thin-wall cover on the ELION 3200-2000. The covers are produced during a cycle of around 4.5 seconds with a 4+4 cavity mold from the company Integrity/Plastisud and a process monitoring system from the Swiss company bfa solutions ltd. The ELION 3200 is equipped with the new aXos control system which has an improved operating panel and numerous new features. ““The ELION 3200 is the epitome of production efficiency, which greatly benefits our customers,” declares Mike Sansoucy, general manager for the brand Netstal. This high-performance machine is based on an innovative hybrid drive concept that combines different drive technologies. The energy-saving potential of hybrid technology is fully exploited using the innovative Eco-Powerunit drive. In comparison to conventional, hydraulically-driven toggle lever machines, the ELION hybrid reduces energy consumption by up to 40 percent.
Excellent growth in business in North America
"The large number of orders for our machines last year was a clear indication that the American market is developing very positively," said Caprio. "We have made a good start to the current fiscal year thanks to the continuing high demand for our products and the very positive feedback from our customers regarding the quality of our machines and services." The company, which has been operating in the USA for more than 45 years, systematically acquired this status over a long period and also geared its product and service portfolio to this market. The result is a complete range of injection molding machines with clamping forces between 40 and 4,500 US tons, including ideally adapted automation solutions. "The technology supplied by KraussMaffei precisely matches the requirements of our customers on the American market," added Caprio. “We will highlight this conclusively with the live demonstration of our machines during the Open House."
Engineering to the power of three
As a third production process, KraussMaffei supplies machines and systems for processing polyurethane. At present, customers are primarily interested in premium quality surfaces, lightweight components and insulation applications. "Components with premium quality surfaces can be produced up to 30 percent cheaper using our combined processes such as ColorForm or SkinForm," stressed JP Mead, Vice President of RPM in US. In addition to a large number of traditional foaming applications, there is also great demand in the area of reaction process machinery in the USA for insulation applications relating to white goods. "Our customers therefore acknowledge the expertise of KraussMaffei in traditional polyurethane reaction process machinery and for applications in the area of white goods," confirmed Caprio.