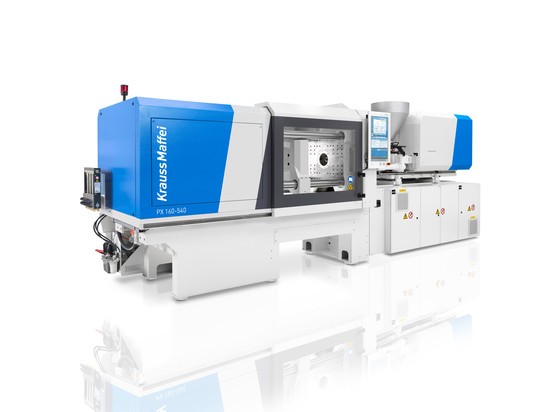
(Florence, KY, September 6, 2017) KraussMaffei Corporation, the affiliate of the KraussMaffei Group in the United States of America, opens its doors on October 4 and 5, 2017. Under the slogan "Our machines shape the world", customers and all those interested will experience a wide variety of live demonstrations, technological innovations and groundbreaking applications from the KraussMaffei, KraussMaffei Berstorff and Netstal brands. For the first time, the well-established event takes place in the new TechCenter at the headquarters in Florence, Kentucky, which has recently quadrupled in size. Numerous technical presentations and booths featuring more than 70 partners round off the program.
KraussMaffei: Premiere of the new all-electric PX series on the U.S. market
With a total of eight injection molding machines currently in production, the KraussMaffei Corporation bolsters its leading position in the North American market for premium quality injection molding machine and system solutions. "In the selected live applications on the new PX and on the CX and GX series by KraussMaffei, we demonstrate maximum productivity and flexibility in all-electric and hydraulic injection molding machines," says Paul Caprio, President of the KraussMaffei Corporation. With its new PX series, KraussMaffei sets new standards in all-electric injection molding machines, because it combines the advantages of an all-electric injection molding machine with maximum modularity in an unprecedented way. "Not only do our customers reap benefits from high diversity and flexibility in the configuration of the suitable machine, for example through our wide range of clamping unit and injection unit combinations, but also in production or in retrofitting", adds Caprio. All machines are equipped with the new enhanced APC plus function (Adaptive Process Control), which ensures maximum process reliability and with it a uniformly high component quality.
On the side of reaction process machinery, KraussMaffei demonstrates its leading system expertise as well. Among the exhibits selected for live demonstration is the RimStar 40/16. The mixing and metering system for polyurethane (PUR) is strictly designed as a modular structure, thus offering maximum flexibility when selecting a suitable configuration. Further highlights include new mold carriers for instrument panel production, glass encapsulation (WinCap) and the production of steering wheels.
Netstal: United States premiere of the ELIOS series and 128 pipette tips in 5.6 seconds
"With both of these top-class exhibits, we are attempting to demonstrate our cumulative systems expertise in fast-running high-precision injection molding applications for packaging and medical technology parts to our American customers", says Caprio. Thanks to its uncompromising design for thin-walled packaging, as well as its clamping unit—the fastest in the industry—the new ELIOS series by Netstal is ideally suited for use in the North American market. The hybrid injection unit equipped with two-valve technology delivers the necessary performance for extreme flow path / wall thickness ratios over 350:1. At KraussMaffei Corporation's TechCenter, interested visitors are able to experience the ELIOS 7500 in action: At a cycle time of 3.9 seconds, round lids weighing no more than 2.8 g are produced from polypropylene in a 24+24 stack mold by StackTeck. Meanwhile, an all-electric ELION 2800-870 produces 128 pipette tips every 5.6 seconds. "With this application, we are focused upon North American producers of disposable materials in medical technology. Apart from pipette tips, these also include petri dishes, blood vials, medicinal beakers and syringes", says Caprio. In the pharmaceutical sector, reputable customers trust in Netstal's expertise as they produce plastic components for insulin pens, lancing devices and sprays on all-electric machines of the ELION series. Using the MED-Kit, a cleanroom class up to ISO 5 can be reached.
Expertise in extrusion technology: Compounding and recycling systems, PVC pipe production and pelletizing in a lab facility
"To the world of extruders, we demonstrate our expertise in pipe extrusion and compounding, technologies highly in demand on the American continent", says Matthias Sieverding, President of the Extrusion Technology Segment of KraussMaffei. Customers and interested parties get to experience several twin-screw extruders in continuous operation, such as the ZE 65 BluePower, with higher torque density and larger available volume for highly filled polypropylene, and the ZE 28 BluePower laboratory extruder, with a significantly expanded process and processing window for color masterbatch. For the recycling of plastic waste, we are exhibiting a ZE 40 UTXi, which produces premium-quality compounds from remnants of fibers and foils—all in just a single step. Additionally, a complete pipe system will produce PVC drainpipes with a dimension of 6" (168 mm) at SDR class 41. The core piece is the KMD 114-32/R twin-screw extruder with the KM-RK 23-250 pipe head, designed for an output of 2,200 lbs/hr (1,000 kg/h). Another highlight of the series is waterless wall thickness measurement.
The KMD 35-26/L laboratory extruder with the KM-GKA 200 pelletizing head demonstrates PVC pelletizing in an exemplary fashion.